Our Products
-
PentoMuls®
-
PentoMag®
-
PentoMag® 2000
-
Pentol Technology for Green Energy Boilers
-
PentoMag® 2550
-
PentoMag® 4400
-
PentoMag® 4410
-
PentoMag® 4450
-
PentoSolv 3®
-
Flue Gas Conditioning
-
Chlorine Conditioning
-
SO3 Analyser
-
SO3 Generator
-
PentoMag® for Cement Plants
-
PentoMag® for Sour Gas
-
PentoMag® for Waste Incinerator
-
Pentol Leak Detection System
-
PCEM-W100: Pentol Humidity Meter
-
PentoMag® for Furnace & FCC units
-
PentoMag® 6200 - High Quality Magnesium Oxide Powder for Industrial applications.
PentoMuls®
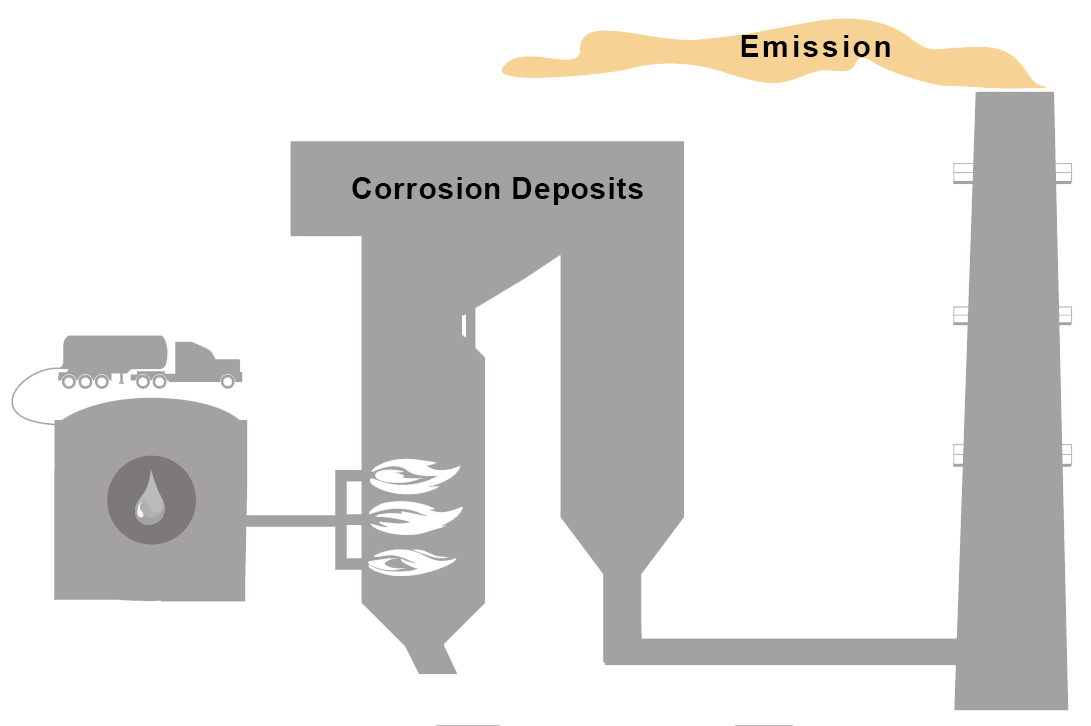
Ideal use cases
Increase net efficiency, Reduce solid emission, Reduce NOx emission
Due to increased usage of low quality fuel oil with high sulphur, asphaltene and vanadium content, power stations all over the world face both environmental and technical problems.
The incomplete combustion of the fuel oil as well as the vanadium and sulphur content cause deposits and corrosions in all parts of the boiler and excessive emissions of solids (particulates) and sulphur trioxide.
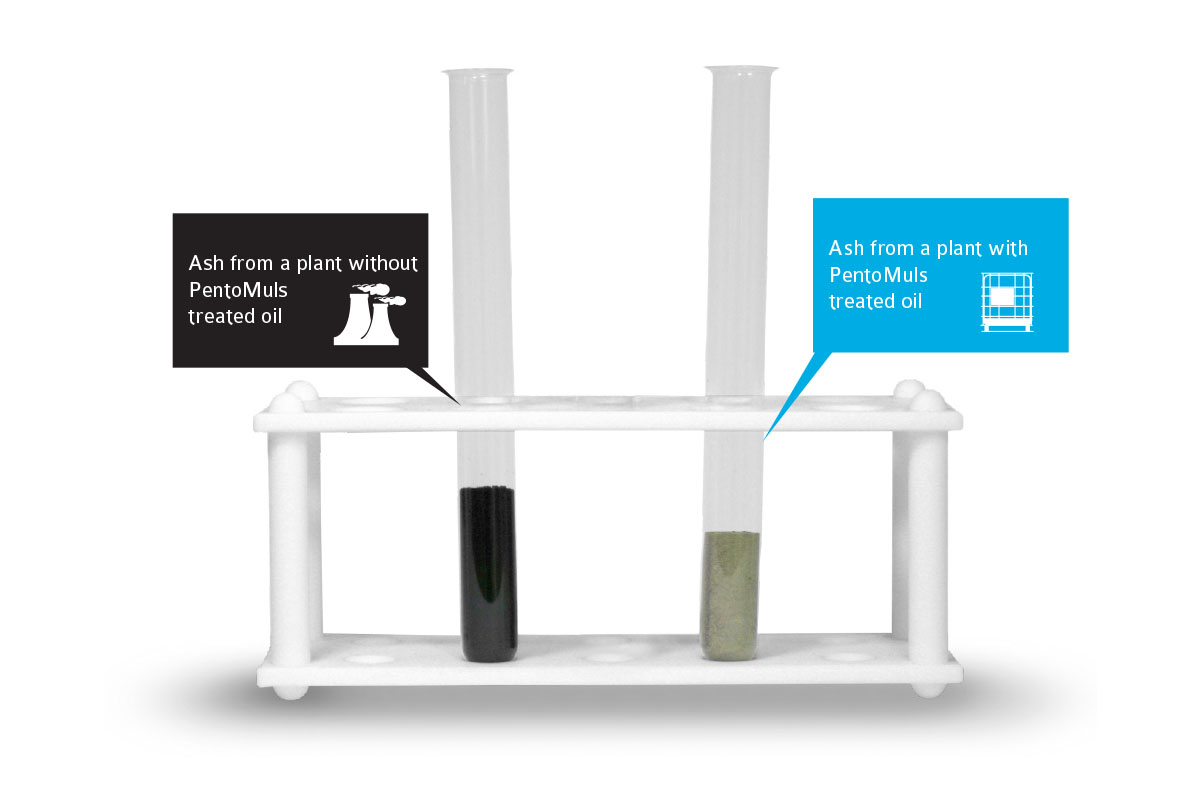
What does PentoMuls® do to my boiler?
PentoMuls® allows the on-line production of a stable water-in-oil emulsion. Firing an emulsion has a great impact on the boiler: Due to the secondary atomization, the fuel oil burns a great deal faster and much more completely. The result is a compact, short flame with a good temperature distribution, therefore much less nitrogen oxide (NOx) and sulphur trioxide (SO3) is generated.
Without water-in-oil emulsion, atomization is insufficient.
The combustion time is too short to burn the oil completely, resulting in unburned carbon leaving the combustion chamber.
With PentoMuls® the secondary atomization cracks down fuel oil particles and allows a complete carbon burn-out within shorter time and a shorter flame.
PentoMag®
Ideal use cases
PentoMag products are magnesium oxide based fuel oil additives designed to fulfil these tasks:
REDUCE CORROSION
PentoMag’s main property is to reduce high and low temperature corrosion. Reduced corrosion means extended life time of high and low temperature sections in the flue gas duct.
REDUCE FOULING
Reduced fouling increases heat transfer in superheater and air heater sections and reduces down-time for cleaning.
REDUCE EMISSIONS
SO3 emission and the visible white chimney plume are reduced.
REDUCE MAINTENANCE WORK
Cleaning intervals for air heater and superheater are reduced. Dosing equipment designed by Pentol is of rugged design and requires minimum maintenance.
INCREASE PLANT AVAILABILITY
Reduced corrosion and deposits mean extended lifetime of high and low temperature sections, allows longer cleaning intervals and less unexpected down-time.
INCREASE BOILER EFFICIENCY
Improved heat transfer, lower O2 and atomising steam consumption, less soot blowing and particularly the possibility to reduce final gas temperature to a minimum, resulting in a substantial increase in boiler efficiency.
PentoMag® 4400
PentoMag® 4400 is designed to fulfill the following goals
Reduce sludge in storage tanks
Reduce waste separation and disposition
Improve combustion of the fuel
Neutralize corrosion effects and eliminate deposits
PentoMag® 2550
Ideal use cases
IMPROVEMENT OF BOILER SERVICE SAFETY
Cleaning a boiler during its outage is a hard physical work, requiring scaffolding to be built inside the boiler and personnel trained for such operation. Application of PentoMag 2550 eliminates most of works hazardous for the service and maintenance personnel.
ADVANTAGES OF ADDITIVES IN SLURRY FORM
Antislagging additives have already been used for many years, initially in powder form. Practical experience was, however, not satisfactory, first of all because of relatively high particle size of powder components (typically 150 microns). The smaller the particle the greater the active surface.
Pentol is the first manufacturer who developed production of fuel additives in form of stable slurry containing micronized active substances in oil suspension. Slurry is also resistant to water (powder will agglomerate in contact with moisture and its efficiency will be strongly limited). Also storage of additives in slurry form is easier and dosing more precise.
HIGH EFFICIENCY OF PENTOMAG 2550
Sophisticated manufacturing and stabilisation of the slurry containing up to almost 70% of active substances enables application of very low dosing rates. In most cases 1 liter of PentoMag 2550 is efficient to treat 50 tons of coal. Actual dosing rate is always adjusted according to practical experience during initial dosing period.
To properly evaluate dosing efficiency the cost of treatment per ton of coal is the key indicator rather than additive unit price
PentoMag® 4450
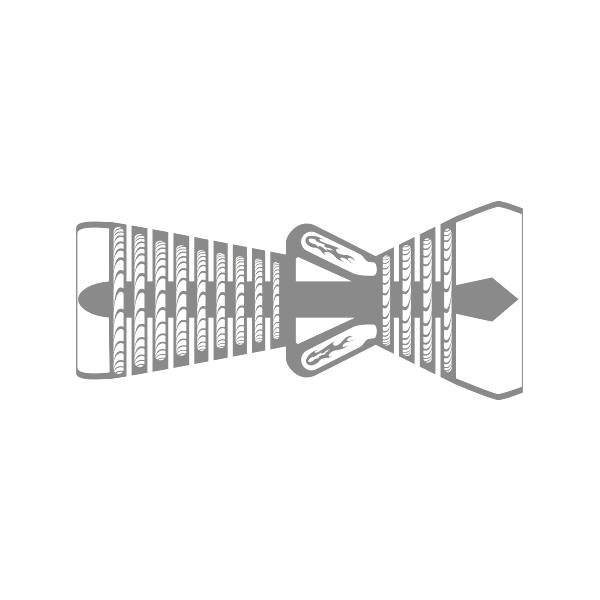
Fuel additives for gas turbines
fuel oil additives to control high temperature corrosion of gas turbine blades and vanes
Pentol offers a range of specially designed fuel additives to control corrosion and fouling of gas turbine components in high temperature section.
Several different corrosion mechanisms can occur from ash deposit formations with low melting point originating from certain metal impurity traces in gas turbine fuels. As a naturally-occurring component crude oils and residual-grade fuel oils typically contain small vanadium quantities.
During combustion, these type fuels create ash deposits composed mainly of vanadium pentoxide [V2O5], and with a low melting point of about 675 °C (1247 °F). At typical gas turbine operating temperatures the vanadic ash deposits melt, and thereby accelerate the blades and vanes surface oxidation rate. Other metal impurity traces, as lead and zinc, will also initiate high temperature corrosion by similar mechanisms.
Read more
SO3 monitoring
Ideal use cases

Pentol offers a range of specially designed fuel additives to control corrosion and fouling of gas turbine components in high temperature section.
In power generation SO3 measurements provide data to allow the operator to burn fuel in the most efficient way to minimize corrosion of the plant and limit acid discharges to the environment. Monitoring of SO3 is also important where it is formed as a by-product, e.g. in De-NOx systems.
In processes where H2SO4 is used or ore with large amounts of sulphur is processed, the SO3 monitor can measure SO4 2- ions and show emission as mg/Nm3 or ppm.
PentoSolv 3®
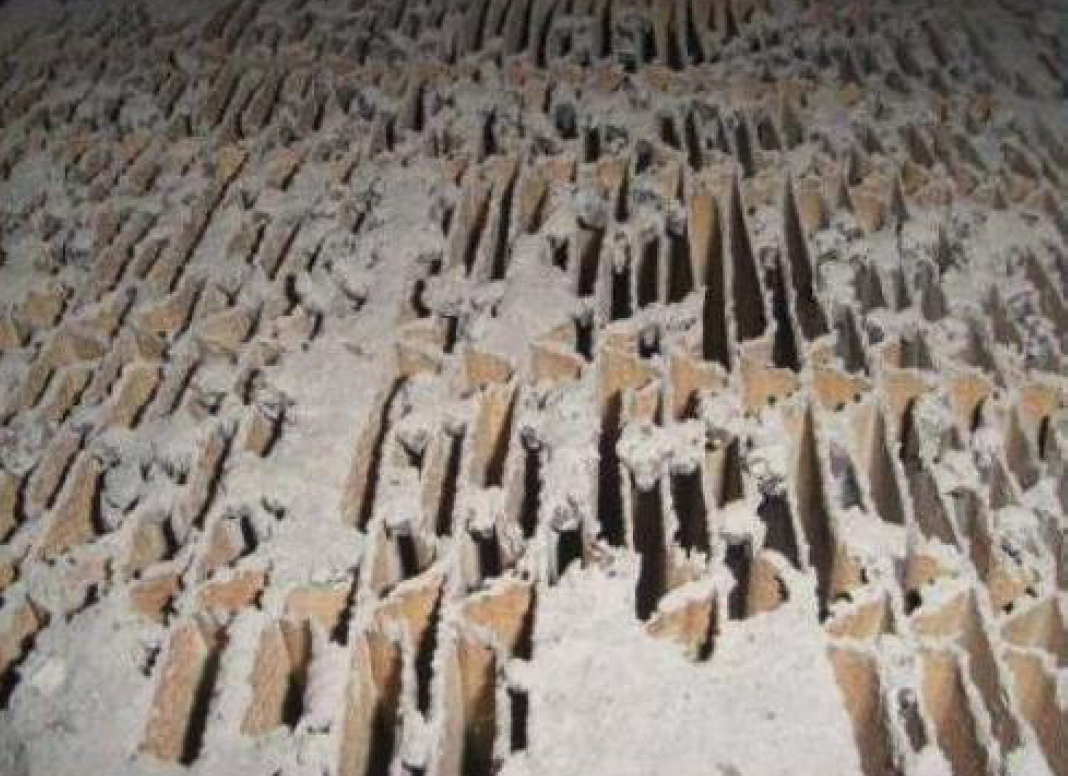
When operating coal or fuel oil fired boilers in power plants, residues of combustion remain inside the boiler and form a solid and adhesive layer of slags. These tenacious and isolating remnants have to be removed regularly in order to ensure an optimal heat transmission on the one hand and to avoid corrosion on the other hand.
Cleaning air pre-heater elements. These elements are installed in high density baskets making it difficult to impossible to clean with water jet or soot blowing.
FLUE GAS CONDITIONING
Ideal use cases
To comply with regulations restricting sulfur dioxide emission, the power industry has begun the switch to low sulfur coals. However low sulfur coal, tends to generate more fly ash and flue gas per megawatt. Because of the higher resistivity of this ash, it is difficult to collect in existing precipitators. Pentol offers Flue Gas Conditioning Systems which increase the efficiency of the existing precipitators, in order to comply with solid emission regulations.
REDUCE FLY ASH RESISTANCE
Reducing the fly ash resistivity, the ESP can work at or even above its design efficiency and collect more fly ash.
INCREASE ESP PERFORMANCE
With the precipitator performing at its design efficiency, sparking and back corona is reduced, extending the lifetime of the precipitator and allowing the operator to run the precipitator on rated performance.
REDUCE EMISSION
Solid emission is widely reduced. With the automatic control system, the Flue Gas Conditioning System of Pentol follows the boiler load and ensures optimal treatment of the fly ash and guarantees best ESP performance.
WHITENESS OF GYPSUM
FGD plants downstream of the ESP receive less fly ash. Therefore the whiteness of the gypsum is incrased, humidity is reduced, allowing the gypsum to be sold at higher price.